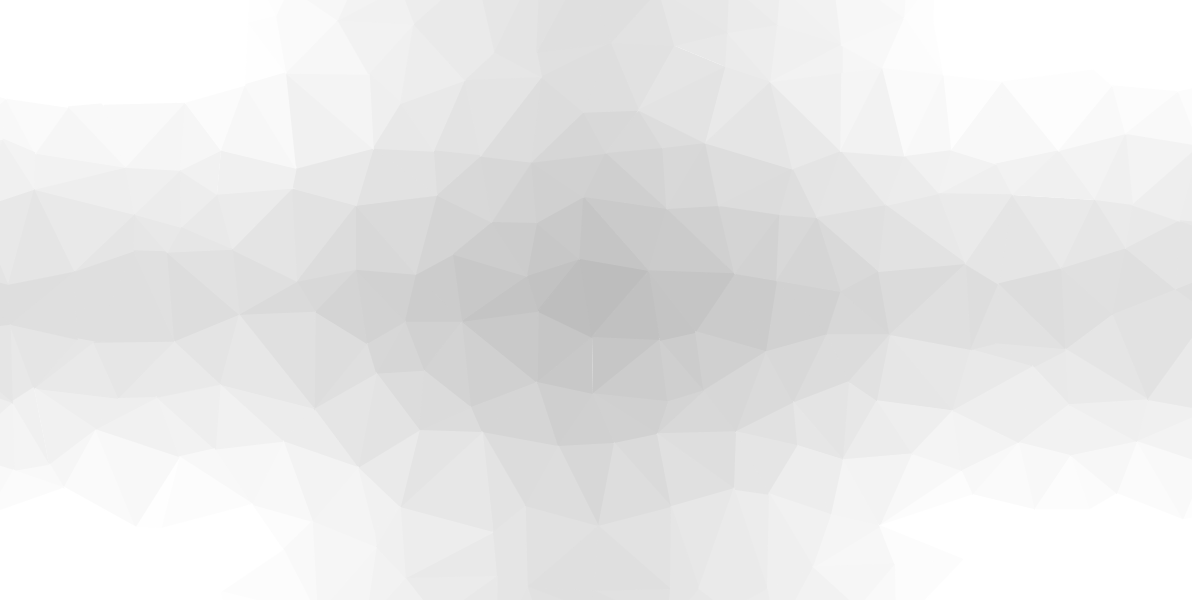
815 Connecticut Avenue
815 Connecticut Avenue (Washington, DC)
Location Washington, DC
Client Owners
Category Office Building
Gross Sq. Ft. 235,172
ENERGY STAR Labeled Building Profile
When Transwestern Commercial Services assumed management of the building, its ENERGY STAR energy performance score was a 38. By utilizing minor lighting retrofits, repairing non-functioning time clocks, and installing occupancy sensors where applicable, as well as tuning the existing HVAC system, the score immediately increased to a 48. After the new central plant equipment was installed during the winter of 2008/2009, the energy performance score jumped to over 80.
Previously, the building's HVAC system consisted of four direct expansion, air-cooled units and an air-cooled chiller. The five large units had been installed in a space that did not provide adequate airflow, causing inefficiency and increased maintenance to be an issue during the entire time they were in place. An older Building Automation System (BAS) was also in place, though it was temperamental and not user-friendly. The air-cooled chiller was used to supply chilled water to the first-floor retail spaces.
A new HVAC system was installed utilizing two 275-ton McQuay "TurboCor" chillers and two new EVAPCO AT series forced-draft cooling towers with Variable Frequency Drives (VFDs). The new chilled water, condenser water, and closed-loop pumps are all variable primary and secondary flow using VFDs. All new chilled water coils and all associated piping had to be installed. MERV 14 rated filters were installed. New dampers with very low leakage rates were installed in the air-to-air economizer section of the building's air handler. McQuay "TurboCor" chillers use frictionless magnetic levitation bearings, are vibration free, and unusually quiet.
Our Solution
Smart Building Technologies designed and installed a new web-based, non-proprietary Building Automation System (BAS) using Tridium products and software to control the new HVAC system.
Utilizing a custom adaptive start-stop program that determines start and stop times based on present conditions and historical start and stop times, building equipment start up and shut down times are adjusted every day. These adjusted times provided a significant savings while still ensuring total tenant satisfaction. When conditions are ideal, Tridium EMS software integrated into the BAS designed by HVAC Concepts, starts supply fans, fully opens the outside dampers and relief dampers, and flushes the entire building with fresh air. This not only flushes contaminates but pre-cools the building, allowing the chillers to start later and save energy.
Project Details
Full EMS retrofit
Integrated using Distech ECY-VAV and ECY-300 Series Controllers
Full Plant retrofit – 2 TurboCor chillers, 2 EVAPCO towers
Fully controlled hot boilers
Fully integrated main AHU with Outside Air (OA) and Return Air (RA) CFM monitoring for LEED
Fully integrated sub-metering for LEED requirements
Perimeter base-board heater controls
Over 200 VAV Controllers
Garage exhaust venting
Real-time monitoring of energy to illustrate granular usage for LEED certification
ENERGY STAR energy performance score was a 38 before EMS retrofit and after full EMS and mechanical (mechanical done by 3rd party) retrofit the score increased to 80
Substantial energy savings realized
Comparing the first 10 months of 2009 to the first 10 months of 2008, the gross cost-per-square-foot decreased by $0.78, even though the cost per KWh increased
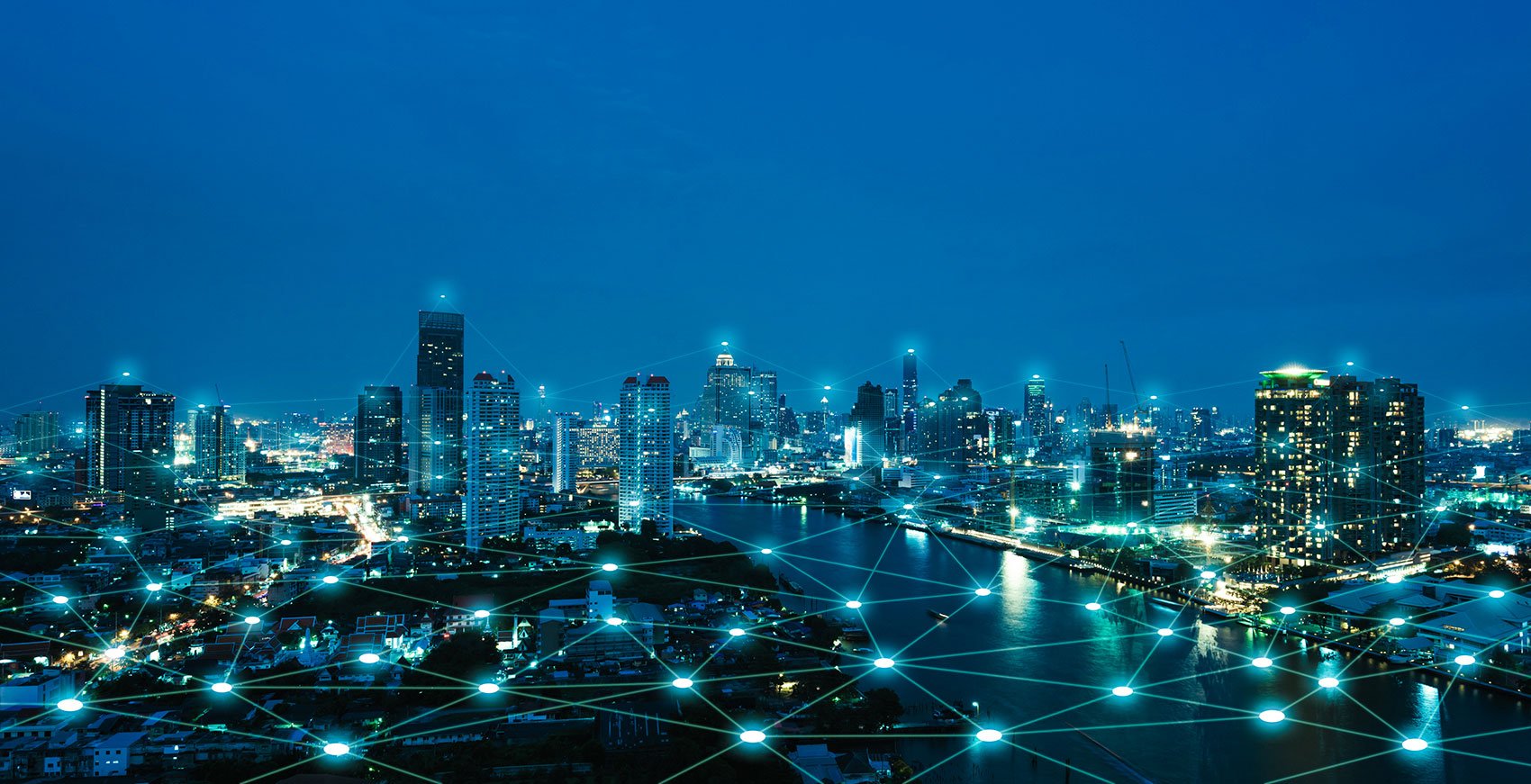